Get an overview quickly!この記事では以下を簡単に学ぶことができます。
●保全性の概要
●保全性の種類
●保全性の決定
保全性とは?
保全性とは、設備やシステムが長期間にわたって正常に稼働する能力を指します。保全性が高い設備は、故障が少なく、安定した生産を続けることができます。一方、保全性が低い設備は頻繁に故障し、生産性に悪影響を及ぼすことがあります。
保全性の決め方
保全性の決め方はの3通りになると思います。それぞれのメリット・デメリットを説明します。
1. 部品ごとの保全性管理
メリット:
- 詳細な管理: 部品ごとに管理することで、個々の部品の寿命や劣化状況を正確に把握できる。
- 予防保全: 部品の摩耗や劣化が早期に発見でき、交換時期を適切に決定できる。
- コスト削減: 必要な部品だけを交換するため、無駄な交換や過剰な在庫を避けられる。
デメリット:
- 管理コスト: 部品ごとの詳細な管理には多くのリソースが必要で、管理コストが高くなる。
- 複雑性: 膨大な数の部品を個別に管理する必要があり、システムやデータベースの複雑性が増す。
- 手間: 部品単位での保全は手間がかかり、頻繁な点検が必要になる可能性がある。
2. 装置ごとの保全性管理
メリット:
- 全体的な見通し: 装置全体の状態を把握でき、トラブルを未然に防ぐための包括的な保全が可能。
- 効率的な保全: 部品単位の管理よりも保全作業がシンプルで、効率的に進められる。
- 一貫性: 装置全体を対象に保全を行うため、システム全体の安定性を維持しやすい。
デメリット:
- コストが高くなる: 装置全体の保全は、必要のない部品まで交換する可能性があり、コストが増大する。
- 過剰保全: 必要以上に保全作業を行うリスクがあり、実際に問題がない部品も交換することになる。
- 装置停止のリスク: 装置ごとの保全には全体的な停止が必要になることがあり、ダウンタイムが長くなる可能性がある。
3. 工程ごとの保全性管理
メリット:
- プロセス全体の最適化: 工程全体の効率性や稼働率を向上させるための戦略的な保全が可能。
- 影響の最小化: 一部の工程だけを停止させることで、全体の生産ラインへの影響を最小限に抑えることができる。
- 柔軟性: 工程ごとに異なる保全戦略を適用でき、最適な保全手法を選択可能。
デメリット:
- 複雑な計画: 工程全体の保全を計画・管理するためには、複雑なスケジュール管理が必要になる。
- 部分最適化のリスク: 工程ごとに保全を行うと、全体の最適化が損なわれるリスクがある。
- コストと時間: 複数の工程を管理するため、保全コストや時間が増加する可能性がある。
保全方式とは
保全性を良くするには次の3つの内どれかの保全方式で管理する必要があります。
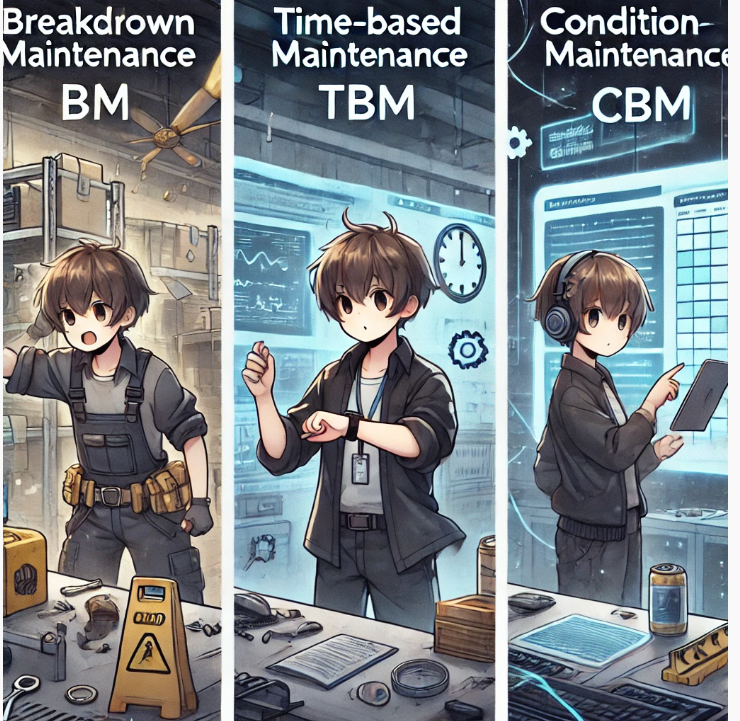
BM(Breakdown Maintenance)
「故障保全」とも呼ばれ、設備が故障してから修理や交換を行う保全手法です。
メリット:保全コストが抑えられること
デメリット:予期せぬダウンタイムが発生しやすく、生産に大きな影響を与える可能性があります。
TBM(Time-Based Maintenance)
「時間基準保全」とも呼ばれ、一定の時間間隔で設備の保守点検や部品交換を行う手法です。
メリット:稼働時間や使用回数に基づいてメンテナンスを行うことで、故障を防ぐことができます。
デメリット:まだ寿命が残っている部品を早期に交換することになり、コストが高くなる可能性あり。
CBM(Condition-Based Maintenance)
「状態基準保全」とも呼ばれ、設備の実際の状態やパフォーマンスデータに基づいて保全を行う手法。
この管理が一番ベストな方法です。
メリット:必要なときにのみ保全を行うため、コスト効率が高く、予防的な保全が可能です。
デメリット:どのデータをどのように取得するか、専門性が高い。
フローチャート(保全方式決定)
筆者の独断と偏見からよく使う考え方を図にまとめてみましたのでご参考ください。
理由等の問い合わせあればXでDMいただければと思います。
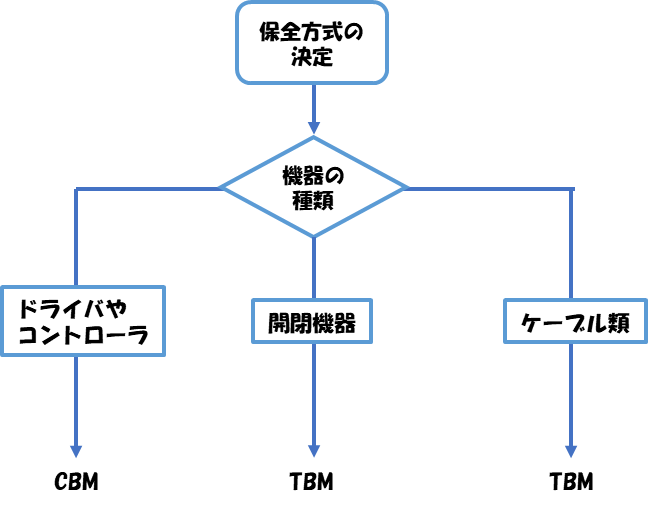
まとめ
BM、TBM、CBMはそれぞれ異なる保全戦略を提供し、設備や運用状況に応じて最適な方法を選択することが重要です。BMはコスト面でのメリットがありますが、予期せぬダウンタイムのリスクがあります。TBMは故障を予防する手段として効果的ですが、コストが高くなる可能性があります。CBMは設備の状態に基づいて最適なタイミングでメンテナンスを行うため、コストと保全性のバランスが取れた方法です。
工場の保全戦略を検討する際には、これらの保全手法の違いを理解し、自社のニーズに最も適した方法を選ぶことが成功の鍵となります。